Quality Purchasing Notes
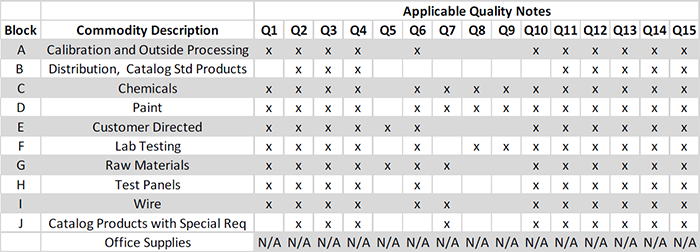
Q1. Quality System – The Seller shall have a Quality System that complies with the specifications of AS9100/ISO9001 or acceptable to Hytek. Hytek reserves the right to verify said system. Neither surveillance, inspection and/or tests made by the Hytek or representatives at either the Seller’s or Hytek’s facility, nor the Seller’s compliance with all applicable product assurance requirements shall relieve the Seller of the responsibility to furnish items which conform to the requirements of the purchase order.
Q2. Notification of Nonconformance & RCCA – Seller must notify Hytek of any nonconforming products verbally and in writing as soon as nonconformance is detected. Seller must obtain Hytek’s written approval for nonconforming product disposition. In response to Hytek-initiated corrective action requests, Seller shall advise Hytek of root cause determination, corrective action taken to prevent recurrence of reported problems and/or discrepancies, and effectively dates of the planned corrective action(s).
Q3. Notification of Process Changes & Obsolescence – Seller must notify Hytek in writing of changes in product and/or process, changes of suppliers, changes of manufacturing facility location, and plans for obsolescence and, where required, obtain Hytek written approval.
Q4. Certificate of Conformance – The Seller shall furnish a Certificate of Conformance with each delivery attesting that each item conforms to all requirements of Hytek’s purchase order and that all required test and inspections have been performed. If a signed copy of the “Supplier Statement of Quality” is on file, a certificate of compliance is not required with each shipment.
Q5. First Article Inspection – The Seller shall perform a First Article Inspection (FAI) of one item from the first production lots required by the Hytek. The FAI shall consist of recorded actual drawing, specification values, and/or requirements (dimensional, test data, processes, drawing notes, etc.) and may be documented on the drawing or on a separate report form. The first article item shall be clearly identified by a tag attached to the item or a label applied to the bag, and a copy of the FAI shall accompany the First Article part. The Hytek reserves the right to verify any or all of the characteristics documented on the FAI report at the seller’s facility.
Q6. Identification & Traceability requirements – The Seller shall provide means of end item traceability as required by Hytek Finishes. The Seller shall maintain the identification and revision status of specifications, drawings, process requirements, inspection/verification instructions and other relevant technical data. Duplication of Lot/Date Code/Serial numbers is prohibited.
Q7. Identification of Shelf Life Material – In addition to the standard identification requirements, supplier must identify each item, package, or container of shelf life material with its manufacture date, expiration date, and any special storage and handling conditions. The supplier must certify that a minimum two thirds of the useable shelf life is available at time of delivery. If exception is taken and approved, it will be noted on the PO.
Q8. Chemical and Physical Test Reports – All purchase orders for chemicals must be accompanied by one legible and reproducible copy of all chemical and physical test reports. The report must contain the title of the authorized representative for the agency performing the test and must conform to specifications.
Q9. Functional Test Reports and Test Specimens – If functional test reports are required, a legible and reproducible copy of the actual test results identifiable with the test parameters and products submitted must accompany the shipment. These reports must contain the title of the authorized representative for the agency performing the test and must conform to specific requirements. Test specimens must be provided upon request for purposes of design approval, inspection/verification, investigation, or auditing.
Q10. Record Retention – The Seller shall maintain records regarding Hytek’s purchase order, specifications, drawings, process requirements, inspection/verification instructions and other relevant technical data. Records shall be maintained by the Seller indefinitely and Seller must obtain written approval from Hytek prior to record destruction.
Q11. Access to Facilities – The Seller shall permit access to the Sellers facility and any sub-tier sellers for surveying/auditing. The survey/audits may include personnel from the Hytek’s, Hytek’s customer representative and/or regulatory authorities, and shall include access to all records applicable to Hytek’s product or orders.
Q12. Counterfeit Parts Detection and Avoidance System Requirements – Seller shall detect and prevent the use of counterfeit, suspect counterfeit, unapproved, or suspect unapproved parts and prevent reentry of counterfeit parts into the supply chain
Q13. Product Safety & Ethics – Ensuring that persons are aware of their contribution to product or service conformity, their contribution to product safety, and the importance of ethical behavior.
Q14. Additional Boeing Requirements: When applicable, suppliers shall conform to all requirements as stated in Boeing Quality Purchasing Data Requirements (X31764). Evidence of conformance must be maintained.
Q15. Product Acceptance – Hytek Finishes reserves the right to approve or specify any designs, test, inspection plans, verification, use of statistical techniques for product acceptance, and any applicable critical items, including key characteristics.